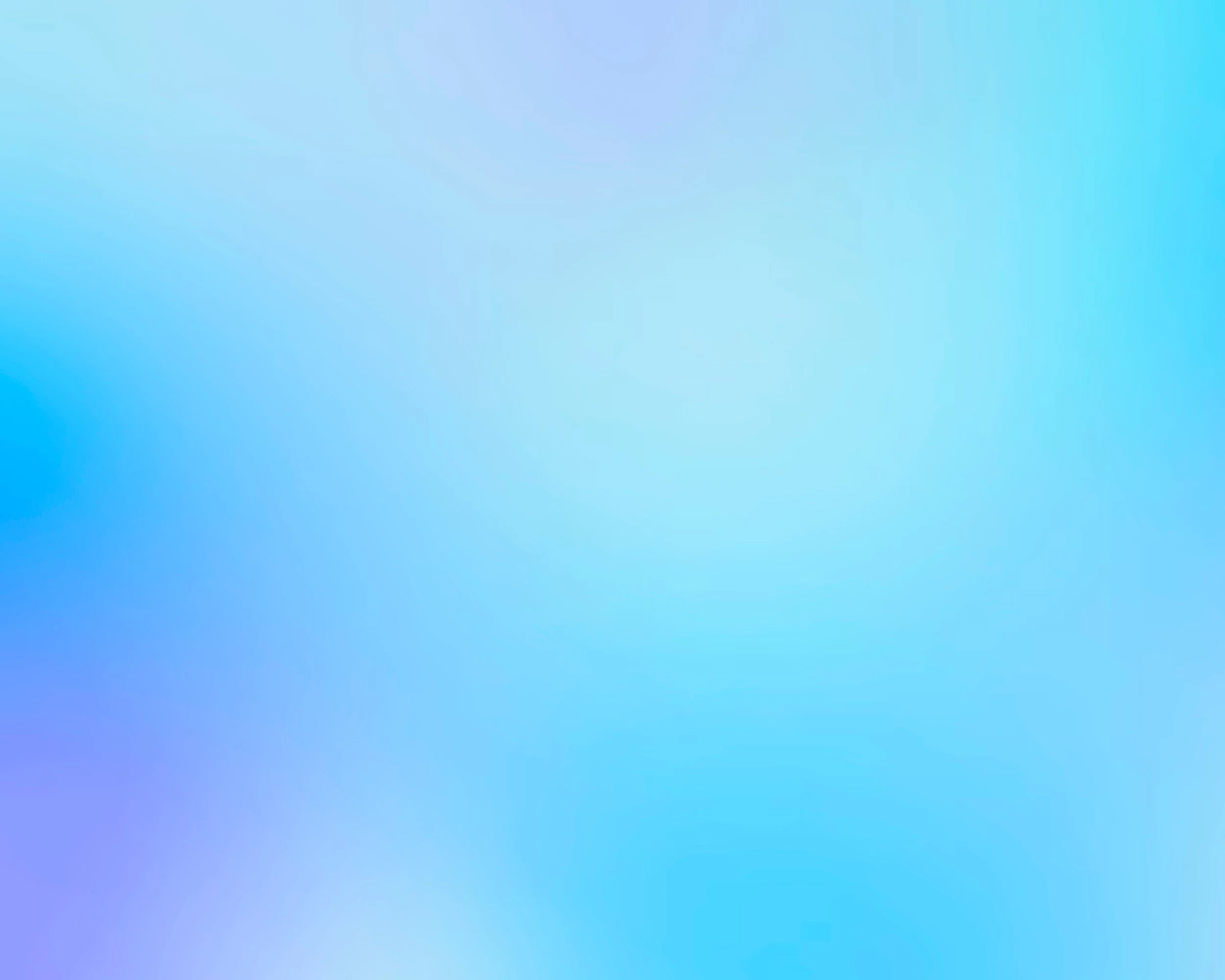
Level 4 Quality Practitioner Apprenticeship
Develop Your Career in Quality Management
Level 4 Higher Apprenticeship Standard Overview
This programme is crafted to develop the capability and confidence needed to implement best-in-class Quality practices.
Specifically designed for professionals working in Quality, it equips individuals with the skills to meet contractual and regulatory obligations while driving continuous improvement in customer and stakeholder satisfaction.
Ideal for roles such as Project Quality Engineers, Quality Assurance Officers, Quality Engineers, Quality Officers, and Supplier Quality Engineers, the Quality Practitioner Apprenticeship supports the development of essential knowledge, skills, and behaviours. This includes understanding Quality strategy and policy, planning and executing activities that fulfil customer requirements, and ensuring effective data collection and analysis.
Quality Planning
Developing and implementing structured delivery systems, such as Quality Management Plans, to ensure consistent, reliable outputs.
Quality Assurance
Ensuring stakeholders have confidence that standards are being upheld through activities such as audits and compliance checks.
Quality Control
Confirming that products or services meet agreed specifications through inspection processes and testing.
Continuous Improvement
Developing and implementing structured delivery systems, such as Quality Management Plans, to ensure consistent, reliable outputs.
Level 4 Quality Practitioner Apprenticeship
Aligned with industry-recognised Quality Standards, the Level 4 Quality Practitioner programme equips learners with the skills, knowledge, and behaviours needed to drive quality excellence across their organisations.
Expertly Designed Learning Delivery
Temple QMS played a key role in shaping the Level 4 Quality Practitioner Apprenticeship Standard and its Assessment Plan. This means our team has a deep understanding of the standard, right from its foundation.
Our training materials were developed through extensive consultation ensuring they are benchmarked against best-in-class practices. This allows us to deliver high-impact, practical learning through our proven blended delivery model.
Our blended learning approach includes:
Tutor-led virtual training sessions
Ongoing 1-to-1 coaching with your dedicated course tutor
Access to comprehensive learning resources and reference materials
Ready to take the next step in your quality career?
Find out how you can join our next Level 4 Quality Practitioner apprenticeship programme.
Work-Based Application to Drive Real Results
Learners apply their training directly to the workplace by delivering an improvement project alongside their apprenticeship. With ongoing guidance and support from a dedicated coach and mentor, each learner builds a portfolio of evidence over the 14-month training period, capturing practical achievements and behavioural development throughout the journey.
What to Expect from the End Point Assessment
Temple QMS ensures learners are fully supported throughout the programme, with tutor-led training, 1:1 coaching, and on-demand access to high-quality learning materials.
During the final 6-month End Point Assessment period, learners will have 22 weeks to complete a work-based Quality Project, demonstrating the knowledge, skills, and behaviours they’ve developed.
The End Point Assessment consists of three components:
Project Presentation and Q&A (50%)
Learners present their completed Quality Project and respond to questions from the Independent Assessor.Professional Discussion (50%)
A structured discussion, underpinned by the learner’s Portfolio of Evidence, assessing how they have applied their learning in the workplace.
Information about Quality Practitioner (Level 4)
-
Understand the organisations operating environment and the factors that may influence its direction and performance, including the markets it operates in, roles and responsibilities, who its stakeholders are and what they require from the organisation. This may include sustainability criteria.
Understand the environment in which the organisation’s products/services are produced or supplied, and the factors that may influence performance, including legislation, customer requirements and regulatory requirements. This may include sustainability or climate change criteria.
How the organisation’s strategy is sensitive to stakeholder perceptions and how this knowledge informs priorities at a tactical level. This may include sustainability, ethical, or climate change related criteria.
How applicable contractual and commercial requirements for quality affect the organisation’s performance objectives for their specific products / services.
The methods and tools for identifying customers/stakeholders and gathering information about their requirements including the tools for analysing and prioritising customer/stakeholder quality requirements using tools such as Kano model.
How to convert quality requirements into performance measures objectives using tools such as Critical to Quality Trees (CTQ Trees), requirements matrices and operational definition.
Risk and opportunity management, including the risk and opportunity management principles, framework and processes, types of risk/opportunity associated with new product/service development and improvement, process and supply chain management and methods and tools for identifying, assessing, and mitigating risks/realising opportunities, such as risk and opportunity register, risk and opportunity matrix, Fault Tree Analysis (FTA), Failure Mode and Effects Analysis.
Products/services life cycle stages (such as Capture, Design and Development, Integration, Production, Support and Closure) and the implication for quality
Concept of process design and how this supports specific organisational objectives using tools such as process flowchart, value stream mapping and SIPOC (Supplier, Input, Process, Output, and Customer).
Tools and techniques for managing the organisation’s specific products / services to meet customer requirements such as Quality Function Deployment, Lean Product Development and Design for Manufacturing.
How to plan, measure, manage and monitor organisation’s quality objectives.
Understand the purposes for auditing and how to plan, conduct, report and follow up an audit.
When to apply a range of business improvement approaches tools and techniques such as Problem definition, measurement systems analysis, Basic data analysis, graphical data analysis, use of software tools for data analysis, root cause analysis, identification and assessment of improvement options, process control tools.
The key considerations (such as political, economical, social, technological, legal and environmental) and approaches necessary (such as Tuckman’s Storming, Norming, Forming and Performing) to enable change in organisations, products or services.
The company’s key drivers for change (internal and external) may influence priorities and objectives.
How to promote the right behaviours to create a quality culture in the organisation and how this leads to organisational performance improvements.
The techniques used for improving awareness and performance in relation to quality objectives and requirements.
Learn how different sources and methods will aid in maintaining own development in the quality profession.
Principles of the foundation of Quality and Quality Management System.
Skills
Identify, interpret and apply relevant legal, governmental or industry regulations affecting the organisation.
Communicate using appropriate methods (verbal, written, visual) to influence internal and external stakeholders, using appropriate questioning techniques such as open questions, leading questions.
Identify, collect and analyse relevant quality data using appropriate tools and techniques such as Pareto analysis, statistical methods and trending analysis.
Apply methods and tools to improve the quality performance of processes, products and services such as production control plans, standardised work, use of failure modes and effects.
Identify, analyse and prioritise quality specific risks and opportunities. Support the development, implementation and effectiveness of resulting actions.
Plan and conduct system, product or process audits.
Assess the effectiveness of the measurement systems using tool such as Measurement Systems Analysis.
Identify requirements from technical documents, commercial input or stakeholder statements and converting to definitions that can drive the organisations processes
Identify gaps in process performance and develop improvement plans to close gaps.
Apply structured problem solving including identification, definition, measurement, analysis, improvement and control methods and tools.
Communicate organisational quality strategy to all levels of the organisation.
Identify who the internal and external stakeholders are and their current and optimal positions (such as hostile, help it work, opposed, uncooperative, indifferent, hesitant, enthusiastic support) required to support quality related activities.
Behaviours
Promote actively best practices and continuous improvement.
Operates diligently with professionalism considering a wider picture.
Act with integrity by being open and honest.
Always put customers at the heart of every task.
Seek continuous professional development opportunities such as self-reflection, gathering information, producing personal development plans and keeping up to date on sector/organisation regulation.
-
Business and administration
-
4
Equal to higher national certificate (HNC) -
14 months
-
£6,000
Maximum government funding for
apprenticeship training and assessment costs.
Enquire Today
Interested in working together? Fill out some info and we will be in touch shortly!